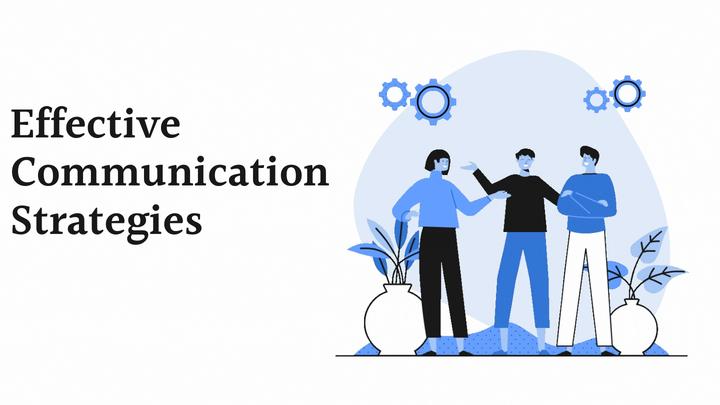
By cuterose
Sound Communication Strategies Improve Workplace Safety
Everysuccessful business is a product of good communication among its team members.That’s especially true in industrialsettings, where a lack of communication can lead to worker injuries, equipmentissues, and even plant shutdowns. However, safety managers may not be familiarwith the many ways that sound communication strategies can set the tone forimproved workplace safety and productivity.
While plantprocesses and Industry 4.0 have advanced with technology, so have thecommunication tools. This article addresses those advancements and clarifieshow good communication processes paired with recent technology improvements mayreduce worker injuries, increase efficiency and productivity, as well as betterengage team members.
Managersneed to be aware of the risks when a cohesive communication plan is lacking.When workers aren’t kept up to date onprocesses and equipment safety, it may increase the risk of incidents. When a hazard is encountered, workers need a means tocommunicate with other team members.
One of thebiggest reasons that communication fails is lack of employee engagement. Whenworkers don’t feel part of a team, they areless likely to do their best. Having a clear communication plan—and asupporting communications technology—ensures that everybody feels connected andaware of what’s going on in theworkplace. The good news is that managers can be on the road to clearcommunication in four simple steps: communicate efficiently, in real time,safely, and with the right people.
Anefficient option for communicating with employees is SMS text messaging, whichsome companies use to notify employees of daily work information and specialconditions, such as a pending snow storm. The communication goes primarily oneway, for example, from the plant manager to employees. It is ideal forall-employee bulletins, but it is difficult to target just the workers on thatnight’s shift.
The two-wayradios common in many industrial settings are another efficient means of workercommunication. They allow workers to communicate with each other, but they donot connect to outside parties, who must have a message relayed by someone witha radio. The nature of FM band radio limits sound quality, and, because it is apublic band, it is susceptible to chatter from driver radios at the loadingdock and other radios outside the facility.
Somelong-range wireless headsets (Figure 1) now use the bluetooth frequency bandaround 2.4 GHz. They have the advantage of high-definition sound and noisecancelling technology. Clarity is key to understanding. Two-way radios arehalf-duplex, which means that only one person can speak at a time. Sometimesthis means getting only half of a message, which could compromise safety. Incontrast, bluetooth and mesh headsets are full duplex, letting multiple peopletalk and listen at the same. Also, they are immune to the signal drops of Wi-Fiand cellular devices.
The environmentshould factor into considerations about which communications technology to use.Because of the ambient noise and physical distance found in many industrialsettings, workers may shout, use hand signals, or read lips to communicate.This style of communication could become a safety issue if there is amisunderstanding. Of course, if workers are wearing face masks, then lipreading is impossible. Workers may seek out a quiet area to talk, but it maynot be safe to walk away from the place where the work is being done.
SMS textworks in all levels of ambient noise. Two-way radios allow workers to talkacross distance and over noise, but usually the radios are hand-held, andworkers may have trouble hearing. In critical situations, this could lead tosafety incidents. Headsets using the latest sound technology make it easier forworkers to hear each other.
Whenworkers encounter a hazard, they need to communicate throughout the facility,to gain assistance or to warn others. Rather than post a handwritten sign or goin search of a supervisor, it is better to immediately report the situation viaradio or wireless communication network. A bluetooth or mesh network providesintercom capability to every person wearing a headset, and via an adapter, itcan also communicate with mobile phones—useful when an off-site manager oroutsider such as a fire chief speaks directly to workers. A communications planshould include employee training, so that workers understand when real-timecommunication is necessary and when it is okay to wait.
Messagessent by SMS text require workers to look at their phones and use their hands, adistraction that could compromise safety, in the same way that distracteddriving leads to highway accidents. Two-way radios let people keep their eyeson their work, although users must push the button to talk. In extreme cases,the time it takes to put down a tool and activate the talk button might not befast enough to warn a coworker of a danger. In comparison, bluetooth and meshheadsets enable instant, hands-free communication.
Meshheadsets are available with ear-muff style hearing protection. Noise reduction ratings range from 21to 26 decibels for standard headsets and 20 to 24 decibels for headsets mountedon hard hats. If workers depend on headsets for doing their jobs, then adoptionof built-in hearing protection is assured.
Workersshould be trained to know which system is appropriate for communicating amessage, and who on that system should get the message, i.e., their departmentor the whole facility. For example, workers should have the ability to easilycommunicate with the maintenance team about a new hazard. Mesh technologyoffers multiple channels, so departments can talk privately on separatechannels or communicate with all team members. The basic range of a meshnetwork is about a half mile, but each headset acts as a node, extending therange.
Bluetoothheadsets connect to each other using an intercom protocol. These networks are limitedto four workers, and are good for small work teams (Figure 2). Mesh headsetsare similar, but each headset acts as a repeater, expanding the network to avirtually unlimited number of people. An adapter, usually worn on the belt, canconnect a bluetooth headset to the more powerful mesh network. Other adapterscan connect the network to two-way radios and smart phones.
Wireless headsetsand two-way radios are affordable, but the cost adds up with the number ofunits. Safety managers can justify their cost on the basis of productivity.Alerting workers instantly about shipments arriving or production changes savestime, making teams more productive. The ability to reach workers with criticalinformation clears up conflicting messages and avoids having to repeatinformation. In an IoT environment, any bluetooth-enabled PLC can be connectedto the mesh network. Spoken alerts can supplement pillar lights, texts, andaudible notifications, enabling workers to quickly respond to issues.
Manychallenges to achieving a safe workplace can be met by delivering bettercommunication. Utilizing the strategies outlined in this article, and havingthe right tools in place, managers can implement a communication plan thatimproves workplace safety and productivity.
Chris Clarke is an industrial communications consultantat Sena Industrial, aprovider of bluetooth- and mesh-enabled headsets and communications solutionsfor industrial and outdoor worksite environments.